Sumio Makino (Advisor, JIRA) 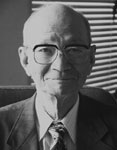 |
1. A brief history of postwar development and an outline of previous installments
I have traced the history of the development of Japanese radiological equipment in the postwar period, and reached the development of MRI at last.
Immediately after the war, the whole country remained devastated by the fires of air raids, and the medical radiological equipment manufacturers were mostly shifted to military industries. Their employees were dispersed, being separated from medical equipment industries.
Among the so-called "major companies", Shimadzu Corp. fortunately escaped war devastation and could start business operation, because it was located in the historical city of Kyoto, which was excluded from aerial bombing. Toshiba Medical Division, which was located in the Kanto area (Kawasaki City), was turned entirely to ashes in the fires. Shortly after that, Toshiba moved its Medical Division to Fuji City, Shizuoka Prefecture, where a textile-manufacturing factory was located. Toshiba recruited the employees who had worked in prewar days and resumed business operation. The small and medium-sized enterprises, especially in Kanto area, experienced the same difficulties amid devastation. They could not get even a sheet of plywood to manufacture a tabletop of fluoroscopic table. Because parts and materials were not available, they could not resume normal work.
Around Showa 25 (1950), when the Korean War broke out, the whole country resumed activity. The Ministry of Health and Welfare started the campaign against tuberculosis, a national disease of those days, by installing clinics nationwide where X-ray tomographic equipment was to be installed for diagnosing tuberculosis. The Ministry instructed each company to increase production of CT. This event motivated full-scale recovery and the development of medical radiological-equipment in Japan.
In the spring of Showa 29 (1954), a fishing boat, No. 5 Fukuryumaru, was exposed to radioactive contamination caused by the U.S. H-bomb test in the Bikini Atoll. A sailor, Mr. Kuboyama, died from radioactive contamination. This event shocked the whole nation, amplifying the so-called radiation allergy among Japanese people more than the atomic bomb damage in Hiroshima and Nagasaki.
In those days, medical radiological equipment was dominated by diagnostic X-ray equipment or therapeutic X-ray equipment. In these circumstances, the U.S. increased production of radioisotopes. Japan also started to use radioisotopes for medical radiological equipment. This became the starting point of the diversification of the diagnostic and therapeutic technologies also in our country.
The administrative and national authorities succeeded to exterminate tuberculosis. As the next step, they started the campaign against stomach cancer, another national disease. Under cooperation of industrial and academic circles, we developed the X-ray TV peculiar to Japan for early detection of stomach cancer. From around Showa 40 (1965), we conducted precise mass screening by using the so-called "ring stand" system. The number of installed equipment in Japan per population became the world's No.1 at a stretch for diagnostic radiological equipment, especially for remote-controlled X-ray TV system.
Around Showa 26 (1951), we started high-energy radiotherapy using radioisotope cobalt 60. This technique was rapidly replacing X-ray therapy. It was a forerunner of therapy by the super high-energy particle beam accelerator, finally leading to the so-called super high-energy particle beam therapy.
The invention of the CT in 1972 was called the most revolutionary invention since the discovery of X-ray by Dr. Roentgen in 1895. It brought many changes to conventional radiology.
Subsequent to this invention, the principle of magnetic resonance invented around 1980 was applied to magnetic-resonance-imaging diagnostic equipment (MRI). In conjunction with MRI becoming popular, high-tech diagnostic imaging became increasingly common.
2. Explanation of the history of development of the related apparatus and accessories in the postwar period
On the other hand, we cannot overlook the history of the development of "the related apparatus and accessories", which also recovered from the devastation of war.
The related apparatus is indispensable to X-ray diagnosis and therapy. For example, they are the X-ray tube, X-ray beam collimator, anti-scatter grid, film cassette, intensifying screen, and X-ray protection material. Immediately after the war, there were not any of these products. Although I was not acquainted with so many people concerned with this industrial sector, I was deeply impressed whenever I was told their stories of recovery from war devastation through the reconstruction of their industry with the Japanese spirit of undaunted efforts.
The subsequent installments of this series will cover the history of their achievement. It is doubtful that I can fully describe it with my poor writing, because their achievement was based on the highest and best efforts; assiduous and painful efforts. But, with permission for the purpose of recording the history of JIRA, I would like to continue this survey and writing.
3. The start of the development of this Association (JIRA) in the postwar period
In prewar days, our predecessors had a close relationship with local and regional doctors in the manufacture, sales and servicing of medical devices, doing group development locally. Such a history was told me by my predecessors, especially by the late Mr. Kuniyoshi Shiiba and the late president Mr. Nobuyasu Iida.
I think that Showa 40 (1965) was the virtual starting point of the new industries association in the postwar period.
In postwar Japan, the health and welfare administration implemented most of the countermeasures against "tuberculosis". Around the year of Showa 40, tubercular problems decreased thanks to the development of pharmaceuticals. As the next step, countermeasures against stomach cancer became the main issue of medical care in Japan. Major manufacturers belonging to JIRA started to shift their efforts from research and development of anti-tuberculosis devices to the development of X-ray equipment for early detection of stomach cancer.
On the other hand, 97 companies were then registered as members of JIRA, and about 90 companies belonged to the so-called "related apparatus and accessory" group. In 20 years after the war, these companies wanted to be an independent industrial sector without retaining small-and-medium-sized enterprises whose main customers are local doctors. They started to develop and popularize their own, unique products.
One of those companies was Mitaya Manufacturing Co. Ltd. whose president was the late Mr. Nobuyasu Iida. (This company is abbreviated as Mitaya in this article.) Mitaya made an assiduous effort in the manufacturing and selling of the X ray grid.
Exactly in this year of Showa 40 (1965), the 11th International Conference of Radiology (the 11th ICR) was held in Rome, Italy. An equipment exhibition was held at the same time. Two Japanese manufacturers, Shimadzu and Toshiba, displayed equipment in their own booths for the first time. I was alone in the booth representing Toshiba. At the exhibition in Rome, I was so surprised that I felt as if scales had fallen from my eyes. I saw the actual condition of the international medical community and industry for the first time, and found that Japan lagged far behind. (Note).
The word "magnificent" used in Japan was quite different from that used overseas. After returning to Japan, I felt in myself that my behavior had become different from what it used to be before.
Note) For details, see "The 11th ICR as a starting station" on page 27 of the 25th anniversary journal of establishment of JIRA.
4. Struggle for the development of the X-ray grid
A. Prologue of the story
1) The first encounter
"The new section manager of Toshiba is a little different from other managers."
In May Showa 39 (1964), an equipment exhibition was held on the occasion of the 23rd Japan Radiological Society conference (chairperson, Professor Ashizawa, Iwate University). One night during the period of the exhibition, Mitaya held an invitation party at a Japanese-style restaurant in Hanamaki spa resort. Mitaya was certainly the first company to hold such a party. I thought that it could afford to do that thanks to the increased sales of products several years after the war. I was called (invited) there, too.
In the previous year (Showa 38, 1963), I was in charge of the development of the betatron and other particle acceleration therapeutic equipment, and cobalt 60 teletherapy equipment, which are related to radiation physics. In April that year, I was appointed unexpectedly as the engineering section manager in charge of diagnostic radiological equipment. I attended the party as the manager in charge of the main stream of the Japan Radiological Society.
Mr. Iida evaluated me in the first encounter, as expressed in the first sentence of this section. Such an evaluation was probably because he noticed that I was free to criticize the arrangement of the Academic society and the Exhibition.
His evaluation, however, became the basis of a lifelong association with him.
2) The second encounter
Although the grid of Mitaya was progressing favorably in the Japanese market, Mr. Iida begun to have basic problems increasingly, and he had to look for improvements. They reduced costs and stabilized quality through an automated manufacturing process. They improved the adhesion of aluminum and lead foil, and focal angled arrangement. Although the first-stage commercialization was successful, he must have been in trouble in achieving the second-stage progress and technical breakthrough.
It was the 11th ICR in Rome in Showa 40 (1965) that we experienced at such a time.
Mr. Iida already sensitive to the overseas situation, wanted to see the ICR himself and decided to go to Rome.
Overseas trips were not common in those days, and no one was accompanying him. He said to me, "Mr. Makino, let's go together." He did not say, "Please take me with you," but it was true that he worried about his first overseas trip and he wanted someone to accompany him.
I went to Spain in Showa 34 (1959) on business, and that time was my second overseas trip.
In these circumstances, I started trips with Mr. Iida, who was agonizing over how to solve the problem of the manufacturing technology of grids.
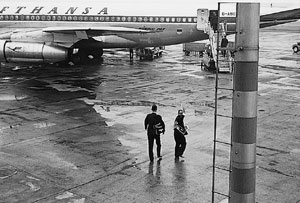 |
|
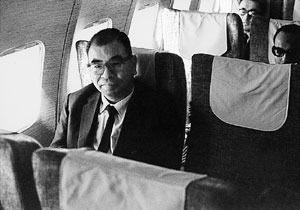 |
Photo 1 Mr. Iida and I at Haneda Airport |
|
Photo 2 In the airplane.
Probably in the midst of a talk about making the grid |
He talked incessantly about the manufacturing technology of the grid, the present situation and future improvement. His talk continued in the airplane going to Rome, in the hotel and in the airplane returning home. Now, I do not remember anything other than talking about the grid. This is the whole story of my trip with Mr. Iida.
Recently, we often hear the words "venture business" said easily. Mr. Iida succeeded in venture business, solely because he devoted his whole life to his business, working day and night. In retrospect, I am heartily impressed that he demonstrated this principle and that he has left a good lesson to us.
B. History of the grid
1) Toward improvement of X-ray image quality
I would like to describe this matter from the viewpoint of the origin of X-rays and the problem of image quality.
The discovery of X-rays by Dr. Roentgen in 1895 is a historical discovery that is known to everyone in our business sector.
Immediately after the discovery, the application research was started in many institutions. In Japan, the experiment of X ray generating was conducted in the next year, 1896.
As application research advanced, how to improve the accuracy and sharpness of the transmissive image produced on the film or the photographic plate became a big problem.
Several researchers made efforts towards that purpose as follows.
a. 1901: Albers Schonberg's compressive cylindrical collimator
b. 1913: G.Bucky's Webenblende (weaving diaphragm)
c. 1917: H.E.Potter's Potter Bucky Diaphragm
d. 1925: Groedel F. M's Groedel method
e. 1926: E. Lysholm's Fine Grid Diaphragm
It was after the Pacific War that full-scale research in Japan started.
Soon after the war, in Japan, we used a "Bucky table" or "Bucky stand" where we vibrated coarse rasters in front of the film to prevent the scattered radiation.
2) Mr. Iida's success in pioneering the business and introduction of the MS grid
During the war, Mr. Iida was dispatched to North China as an army civilian employee.

- Showa 21 (1946)
He founded his business as a subcontractor for the machining of parts of X-ray equipment and other electric parts. He expanded the scope of business gradually to manufacture the fluoroscopic tables and X-ray tube support units (that was called "Stativ" in German) at the request of Osaka Roentgen-rays Manufacturing Co., Ltd. Despite the small number of employees, his company started to manufacture comparatively large-sized equipment to enter the medical device market and attempted to graduate from being a subcontractor business.
- Showa 23 (1948)
When Mr. Iida attempted to graduate from being a subcontractor business to develop and commercialize products, he was encouraged by the late president Mr. Motomu Watanabe of Goto Fuundou Co., Ltd. (who founded "Japan Medical Electric Equipment Association", JIRA's predecessor, and also acted as a matchmaker for Mr. Iida). Mr. Watanabe highly evaluated Mr. Iida's effort and technical capability and recommended that Mr. Iida should manufacture independently and sell the Bucky Blende (diaphragm), which was imported at that time. On that recommendation, the Bucky Blende was manufactured and had finer rasters, an innovative mechanism for the vibration of rasters, and many other improvements. It was equal to or better than the products of five competitors in Japan. Especially, the in-house development of the raster contributed to improve its quality and to shorten the manufacturing time, resulting in high popularity.
- Showa 25 (1950)
Mitaya and Mr. Iida did their best in the manufacturing and selling of anti-scatter Bucky and its Blende. They made further efforts to increase the accuracy of the raster and to develop an anti-scatter grid.
From that time, Mr. Iida and the employees continued efforts in research.
They imported the bakelite-made grid from Lucidex, U. K. and were surprised to see its accurate adhesion of transparent materials and lead foil. They also imported the neat grid using aluminum as a spacer from Elema Schoenander, Sweden and were impressed with its accuracy. Mr. Iida and all the employees determined to make a competitive product and set the goal for success.
Mr. Iida wrote about their effort and struggle against difficulties as follows.
"Soon after the war, we made the wooden raster that had a coarser texture than the grid to mount on Bucky. At that time, suitable materials were not available, and we had many difficulties. We attempted metallikon where lead was sprayed on aluminum, but we failed. So, we shifted to an adhesion technique. We prepared various kinds of adhesives and conducted the heating test until midnight. The bitter experience is now remembered nostalgically." (see JIRA Bulletin No. 145. page 63.)
- Showa 28 (1953)
Mitaya finally decided to use aluminum as the transmission material and lead foil as the absorbing material. They investigated quickly the domestic and foreign patent information, applying for a utility model right. This application was publicly announced as No. 415937 in 1954.
- Showa 30 (1955)
The time to launch a new product came in April of this year.
The 14th Japan Radiology Society conference was held in Kyoto. Mitaya's grid was called an "all-metallic anti-secondary scatter grid" and was exhibited at the concurrent exhibition. The chairperson of the conference was the late Professor Goro Goto (1894-1989) of the Kyoto Prefectural University of Medicine. He used the grid experimentally in advance and extolled the result as follows.
"…I used the Mitaya grid prototype that was invented through Mr. Iida's research effort of several years experimentally. They succeeded in solving all the problems in the manufacture of the Lysholm Blende. The grid shadow on film is almost invisible even under close observation. The interval is uniform without any unpleasant stripes. Adhesive materials are suitable to ensure complete flatness and do not cause any distortion of image. The absorption of primary X-rays is very small. The overall performance is excellent, and the price is less expensive than foreign products. It is a great achievement for the radiology community and industries in Japan. I would like to express my hearty congratulations.
I would like to recommend that all the radiologists should use this grid…" (see ditto, page 62).
"The exhibition was a good chance to demonstrate our effort to the radiology community. The product was highly appreciated as a result of our long-time effort in trial and error. As one of the staff members, I recollect it even now with pleasure…" says Mr. Minoru Kamoshita, who worked for Mitaya since its foundation and is 70 years old now.
Thus the Mitaya grid, called MS grid, was launched successfully into the market.
C. Development of the grid
1) Introduction
In Part 1, I briefly described my first encounter with Mr. Iida of Mitaya, the establishment of his business, his effort to improve grid performance, and the start of export business.
Every industrialist made a painful effort in recovering from war devastation and contributing to postwar reconstruction. But, Mr. Iida is typical and remarkable, representing our history. In that sense, his achievement is worth recording as follows.
In this Part 2, I describe the effort made by Mr Iida and Mitaya’s staff in research and manufacturing, including the theory of technical analysis of the X-ray grid.
2) Mitaya Grid (brand name: MS Grid): Reward for the effort and road to success
In the early postwar period, Mitaya manufactured the "Bucky Blende" that was used as anti-scatter grid. The raster, which was called "Blende", had coarse stripes, and it was moved right and left in order to obscure the stripes and remove the scattered X-rays.
Around 1950 to 1951, Mitaya continued to manufacture Bucky Blende. However, they thought that a large Bucky apparatus would be unnecessary if a high-performance grid can remove the scattered X-rays. In order to develop such a grid, they imported foreign products that were rarely available at that time. They analyzed the bakelite grid made by Lucidex, U.K. They obtained the aluminum grid made by Elema Schoenander, Sweden. Mr. Iida decided to adopt the aluminum grid and paved the way for further research.
About the adhesion technology of this aluminum and lead, Mr. Iida made a great effort in research as mentioned in Part 1. "In the process of an experimental work, all the employees cooperated with President with overnight work" reminisces Mr. Minoru Kamoshita, the present top employee.
Composition of aluminum and lead foil resulted in a new Mitaya grid which was called the "full metallic anti-secondary scatter grid". The grid was exhibited at the concurrent exhibition for the Japan Radiology Society conference held in Kyoto in 1955. The chairperson of the conference, Professor Goro Goto used the grid prototype experimentally in advance and extolled its excellent performance publicly. This was the time when "MS grid" obtained social status. (For details, see Part 1.)
3) Progress to diverse products and higher accuracy
"MS grid" enjoyed a good reputation at the Japan Radiology Society conference. After that, it was highly evaluated also at the Japanese Society of Radiological Technology conference. It was a great event to facilitate market development. The grid that won a good reputation was a parallel grid of 28 lines per centimeter, and the size was 10" x 12" (Figure 1). After the announcement at the conference, opinion was exchanged with radiology-related persons, who gave us much advice and many proposals.
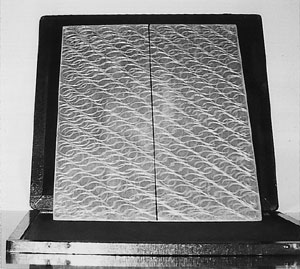 |
Figure 1 The First Product (10" x 12" sized grid) |
The market demanded the focused grid instead of the parallel grid. X-ray equipment manufacturers demanded diverse sizes.
In the meantime, in order to improve the quality and stabilize product performance, replacement of manual work by automation was essential. For that purpose, further efforts towards better manufacturing technology became the goal of all the employees.
At this stage, as mentioned in Part 1, Mr. Iida was preoccupied with automation of the focused grid, selection of pasting materials, and the study of quality control techniques. Mr. Kamoshita, the top employee, told me the following episode of Mr. Iida's life in those days. It is "When the President went missing."
"Late in the evening while they were attempting to manufacture their own focused grid, Mr. Iida went missing suddenly.
Mr. Iida said that he went out after telling it to his family. But, the family members replied that they knew nothing. The worried employees could not go home even after an evening’s overwork. The family members also worried about him. Even on the next day, he did not telephone and everyone worried all day long.
Late at night on that day, he returned smiling and holding something in his right hand.
He said, "I happened to have a good idea last night. I went to a weaving machine factory in Kiryu City, Gumma Prefecture, where I got 'a guide gear' (reed). With this as a hint, let's design an assembling machine. I found this at last after visiting many places in Kiryu City. By the way, are you still working late at night?"
In response to his last utterance, everyone who worried all day long said, "No kidding please, President."
Note: "a guide gear" is an essential tool for a weaving machine. It is like the enlarged model of an ideal grid. The X-ray transmission portion is space, and the X-ray absorbing portion is a thin sheet of iron. It is quite understandable that Mr. Iida spent a whole night to find it.
4) Struggle for diverse model production, stable and better product quality and shorter production process time
The following is the process of development of the "Mitaya grid" based on the data of Mr. Kamoshita, a Mitaya employee
- The start of marketing
In 1955, Mitaya delivered to the market the first grid with the following specification: parallel type, 10" x 12" size, grid density of 26 lines /cm and grid ratio of 5:1. The grid that was extolled by Professor Goto at the Kyoto conference had 28 lines /cm.
After the conference, the Mitaya grid became very popular with its rigid structure, ease of use, and high anti-scatter performance. The orders for the grid increased, even resulting in the problem of delivery delay.
- Maintenance of production and knowledge
In 1960, Mitaya began the full-scale production of the so-called angled grid with grid density of 26 lines/cm, grid ratio of 8:1, and focus distance of 100 cm and 150 cm, Later in response to the demand from those manufacturers, they changed the number of lines per centimeter to 28. This change of larger number of lines became a big hint for subsequent production of the high-density grid.
They developed concurrently the focused grid, reached the stage of commercialization, and improved their production line. They were very busy in substantiating and improving an order taking system and a production system in order to cope with the rapid increase of orders and the diversification of products types.
At this stage, they created an explanatory booklet (Figure 2) entitled "MS Lysholm grid" based on the recommendation by the Japan Association of Radiological Technologists and the Japanese Society of Radiological Technology. They distributed this booklet to the visitors at every exhibition held concurrently with academic conferences during the period of 1960 to 1964. Moreover, in response to requests from customers, they published a book entitled "Radiography and scattered rays" (Figure 3) coauthored by Tsutomu Sugawara (Kyoto University) and Minoru Nakamura (Mie University), and presented this book to the radiology community. It was welcomed as a professional book in this field.
- Progress to the international market
As mentioned in Part 1, after visiting the international conference in Rome in 1965, Mitaya started transactions with the U.S. Lieber Flasheim Inc. in 1967. Now, it has transactions with six U.S. companies and other companies located in Australia, Sweden, France, Spain, Italy, Denmark, Israel, Slovenia, China, Hong Kong, and Korea.
At the Radiological Society of North America (RSNA) conference in 1983, Professor Kunio Doi (University of Chicago) presented a research paper entitled "Removal of scattered radiation by the high-density grid", reporting on the effect of the removal of scattered radiation using the Mitaya MS grid.
This report was highly estimated by RSNA and granted an award by RSNA (Figure 4).
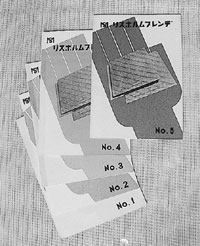 |
|
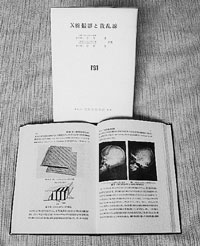 |
|
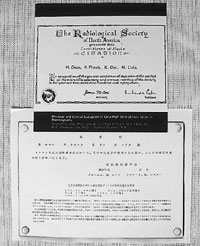 |
Figure 2
An explanatory booklet of Lysholm blende grid |
|
Figure 3
A book entitled "Radiography and scattered rays" coauthored by Professor Sugawara and Dr. Nakamura |
|
Figure 4
RSNA award granted to Professor Doi |
- The challenge to automation of production equipment
(1) The problem of thickness measurement of basic materials
As a prerequisite for production automation, it was necessary to keep constant the thickness of basic materials: aluminum and lead foil. They attempted the methods of several companies. The external pressure measuring method left a measurement trace on the raw materials. In 1968, they cooperated with Company S.S., adopting the non-destructive testing method, and attempting many experiments until commercialization, and finally succeeded in the automation of thickness measurement.
(2) Introduction of a compound material distribution machine
Aluminum and lead foil are integrated into a compound material. It is then cut into bands to make the grid material. In the cutting process, a mixing machine was used to make the cut section uniform visually. This machine was called a distributor (Figure 5). The surface of cut section shows the individual characteristics of grid compound material, slight difference of thickness, difference of hardness of material, change of sharpness of blade, etc. If the difference is transferred to the lamination process, then it causes "unevenness" and "variation" on X-ray film. It affects the internal product quality of grid. Introduction of the distributor solved the problem, producing the uniform parallel structure, and achieving the expected goal.
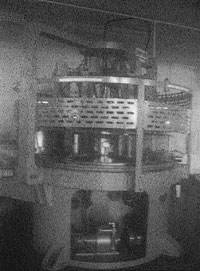 |
Figure 5 Grid compound material distributor (Because this machine is confidential to outsiders, the photo is intentionally blurred.) |

5) The present product group of Mitaya (Table 1)
The Mitaya products were developed as described above. They are now available in diverse types. Table 1 shows how they increased types of products.
Table 1 MS grid available in diverse types
MS grid chronicle
Fiscal year |
Product name |
Specifications and features |
1955 |
Parallel: 26 lines/cm |
5:1, 10"x12" size, brand name: MS Lysholm blende |
Parallel: 28 lines/cm |
5:1, 6:1, 10"x12" size, 11"x14", 14"x14" |
1960 |
Focused: 26 lines/cm |
6:1, 8:1, for Bucky |
Focused: 28 lines/cm |
8:1, 10:1, for Bucky |
Cross: 28 lines/cm |
Parallel type grid, orthogonal cross, 10:1, 12:1, |
Circular: 28 lines/cm |
Initial grid for I.I, according to maker's specification |
1963 |
Curved-surface: 28 lines/cm |
For mirror camera 90cmR, 5:1. according to maker's specification |
1985 |
Focused: 34 lines/cm
Parallel: 34 lines/cm
|
For direct: standard specification, maker's specification, various kinds for Bucky
For direct: standard specification
|
Focused: 40 lines/cm
Parallel: 40 lines/cm |
For direct: standard specification, maker's specification, various kinds for Bucky
For direct: standard specification
|
Focused: 60 lines/cm |
For stationary: standard specification, maker's specification, brand name: Microfine |
Microreader type 101
Microreader type 201
|
60 lines/cm grid stationary use radiographic table
60 lines/cm grid stationary use radiographic table - grid exchange type
|
Curve: 34/40 lines/cm |
Cassette incorporation type, focus 65cm/90mmR |
Long: 34/40/60 lines/cm |
Two or three plates adhesion, size: within 48x144cm |
Circular: 34/40/60 lines/cm |
According to maker's specification |
1986 |
Mammography: 80 lines/cm |
Super high density, carbon cover, stationary use for biopsy |
1989 |
Carbon cover |
Corresponding to various products, dose reduction, increased strength, grade up product |
1992 |
Compressive board
combination : 60 lines/cm |
For changer device, Incorporation of compression board and grid increases image quality |
1996 |
Bedside : 34/40 lines/cm |
3-P type, 3:1, grid specification for minimum exposure and cut-off |
1998 |
CR-DR : super high density
80 lines/cm |
Corresponding to accuracy required by specifications of various companies |
1998 |
Animal use : 34 lines/cm |
6:1, Carbon cover improves image quality, durability and drug-resistance |
2001 |
Cap type
for standard type cassette |
34/40/60 lines/cm, Improvement of operability of long type grid.
Increase of rigidity of grid body and operability for routine radiography |

6) Estimated market of Mitaya grid "MS grid" (Figure 6)
Market situation in domestic and overseas markets
April, 2002
|
Manufacturer's name |
Country |
Intermediate material |
A |
Mitaya |
Japan |
Aluminum |
B |
Schmidt Roentgen Rays |
Netherlands |
Fiber |
C |
JPI |
Korea |
Aluminum |
D |
Seibu Techno |
Japan |
Aluminum |
E |
SOYEE |
Korea |
Aluminum |
F |
Elema Schoenander |
Sweden |
Aluminum |
G |
Giladoni |
Italy |
Aluminum |
H |
UMI |
Korea |
Aluminum |
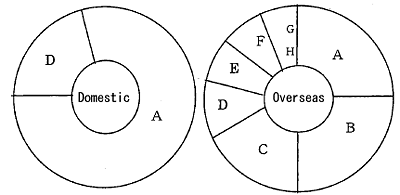 |
* Estimated market share of each manufacturer
(estimated quantity) |
Summary
These two installments describe the achievements of Mr. Iida.
I would like to thank President Mr. Motohisa Shimura and Mr. Minoru Kamoshita for their great cooperation in editing this article.
Regrettably, the death of Mr. Nobuyasu Iida was soon followed by that of Mr. Noboru Iida.
While writing this article, I had a clear recollection of both gentlemen, and was impressed again with their achievement with my eyes shut.

Chairman Mr. Iida's award history
(1) 1975: Governor-of-Tokyo commendation for achievement related to science technology research
(2) 1976: National Medals of Honor, Medal with Dark Blue Ribbon
(3) 1977: Invention Grand-prix, Fukuda Award from Japan Society of Advancement of Inventions
(4) 1982: Governor-of-Tokyo commendation for achievement related to Pharmaceutical Affairs Law
(5) 1983: National Medals of Honor, Medal with Yellow Ribbon
(6) 1987: Governor-of-Tokyo commendation for achievement related to health and sanitation
(7) 1999: Conferral, The Order of the Sacred Treasure, Gold and Silver Rays
The history of Mitaya, representative of the development of this Association, is too comprehensive for me to describe with my poor writing. If this article would be read by people of the future generation as a record of the struggle made by a member of JIRA, then I would be very happy.
The story is worth recording as the first chapter of the history of struggle in the medical imaging industry.
|